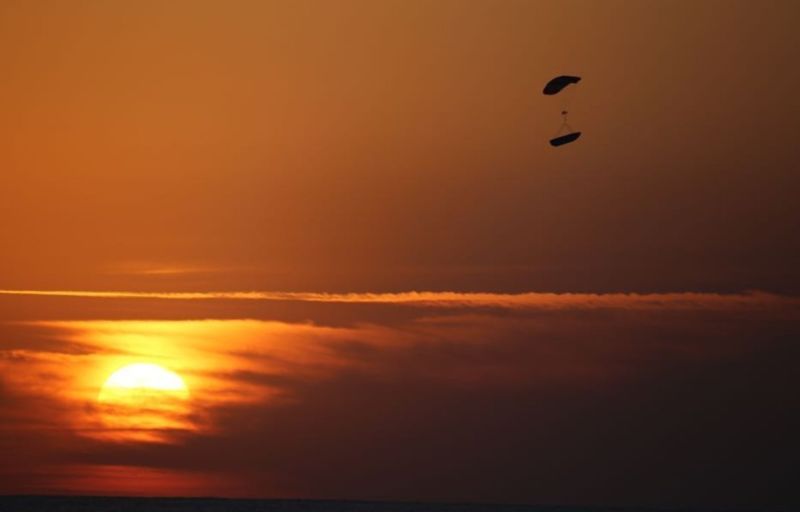
Elon Musk/Instagram
Amid much fanfare, SpaceX began landing its Falcon 9 rockets in 2015, and began using them again two years later. The Falcon 9 rocket’s first stage, with nine engines and most of the mass, is half the cost of building a single rocket, so it saves SpaceX significantly time and money.
However, like other boosters, the Falcon 9 rocket has two main components. There is a second stage, which boosts a payload into orbit, and for most missions, a payload fairing that protects the satellite as it passes through the atmosphere. SpaceX briefly explored recovering the Falcon 9’s second stage, but concluded that it was not possible without major modifications that would drastically reduce the rocket’s payload capacity.
But what about the payload fairing? Unlike papier-mâché, these are constructed in two pieces through a laborious process of stacking composite materials. Manufacturing the fairings is time-consuming and costs about $6 million to manufacture both parts.
Go get them
Years ago, SpaceX founder Elon Musk challenged his employees to go grab a fairing. “You have six million bucks falling out of the sky,” Musk famously said. But how to do it?
At first, the company’s engineering team argued that they should be caught with a net before they hit the ocean, said Kiko Dontsev, SpaceX’s vice president of publishing. Dontsev spoke about the fair rescue effort during the „Summit At Sea” program earlier this year. Video of his speech Available on YouTube.
The concern among engineers was that exposure of the fairing and its delicate electronics to seawater would cause significant corrosion. They believed this would render parts of the fairing unusable. So the SpaceX engineering team developed a complex recovery process, and the company caught its first fairing in January 2020.
Kiko Dontchev/SpaceX/YouTube
„You’re basically this amazing algorithm, this crazy automation,” Dontsev said. „There was a parafoil on the fairing that would steer itself, and then the boat would have this automatic control that would basically turn and follow. And both would close. That’s how you catch them. It worked. We did it.”
As weather was a major factor in the Atlantic Ocean, it did not work properly.
„The truth is, most of the time, it’s a hot mess with 7- to 9-foot waves, very short duration and a ton of wind,” Dontsev said. „So even if we caught it once, our actual success rate of bringing the fairing home was very low. It was 50 percent, less than 40 percent. Our ability to prepare to fly was stifling our launch rate.”
Simplifying the process
As part of his talk, Donchev talked about the „algorithm” that SpaceX uses when designing new technology to solve problems. Basically, it provides a blueprint for innovation.
„When you fundamentally invent a new technology, you’re wrong,” he said. „It’s a question of how wrong it is. Because your ability to learn is constantly changing. So you’re definitely not going to end up where you started.”
The algorithm starts with two steps: „Make the requirements less dumb” and „Eliminate the part or process step.” This requires engineers to think outside the box and challenge existing requirements. Ask if they are solving the right problem.
Kiko Dontchev/SpaceX/YouTube
As for the exhibits, the problem was catching them before they fell into the sea wrong problem The ok The problem was retrieving exhibits and updating them quickly for flight.
„What we discovered is that the fairings float very well,” Dontsev said. „Like a sailboat, they’re composites. It’s really a big boat. Well, do we really have to hold them? We challenged that requirement. We moved some sensitive areas to a higher part of the exhibit.” This allows the fairing electronics to survive, even if the fairing takes on some water.
Put it all together
The SpaceX algorithm consists of five steps. Basically, Dontsev said, do the first two steps as many times as necessary before moving on to the final three: optimize, accelerate and automate.
With the exhibits, the company finally completed the second step with sea-based recovery. It had a very simple structure, with a fixed rescue vessel and a crane for fishing out to sea. This allowed the company to go from a low success rate to a 99 percent success rate recovery. They can be quickly updated and returned to additional missiles within weeks.
But this created a new problem. Where to put it all?
„We have more fairing than we have room for,” Dontsev said. „Fairings are the one thing we don’t even talk about when it’s time to start. They’re always ready, no problem.”
„Oddany rozwiązywacz problemów. Przyjazny hipsterom praktykant bekonu. Miłośnik kawy. Nieuleczalny introwertyk. Student.